In an era where environmental protection is an essential priority, we work daily to minimize our environmental impact and offer innovative and sustainable solutions.
Through cutting-edge practices, we have learned how to combine production efficiency, environmental responsibility, and people’s well-being. We have created a circular economy to recycle and reuse every piece of ceramic we produce. Within our production cycle, we keep materials carefully separated to preserve their purity, allowing us to reintegrate unfired materials—such as broken or non-compliant pieces and powders—back into the raw material.
And if they are already fired? Fired materials that do not meet quality standards are ground down, turned into powder, and then used to produce non-precision refractory materials, destined for fireplaces, barbecues, or pellet stoves.
Circular economy is not limited to ceramic processing. In recent years, we have implemented centralized extraction systems for each operator and workstation, with suction points at every bench. This allows us to maintain constant air circulation and capture even the finest dust particles generated during production, which are then reintegrated into the manufacturing process.
Thanks to a circular model, we turn waste into valuable resources.
In our industry, water is one of the most used resources. Thanks to a closed-loop system, we can eliminate water waste by recovering and reusing the water already introduced into the production process. For example, the water used in machine cooling circuits is cooled through advanced air-based systems and then reused for cooling, completely eliminating wastewater discharge.
Zero-impact ceramics.
Ceramics are a durable and resistant material, even in extreme conditions, though their lifespan naturally depends on usage conditions. By nature, ceramics do not degrade but may experience wear or erosion due to the environment in which they are used.
Ceramics have a very long lifespan, and replacements are usually made as a preventive measure. This makes ceramics a green material that is 100% recyclable.
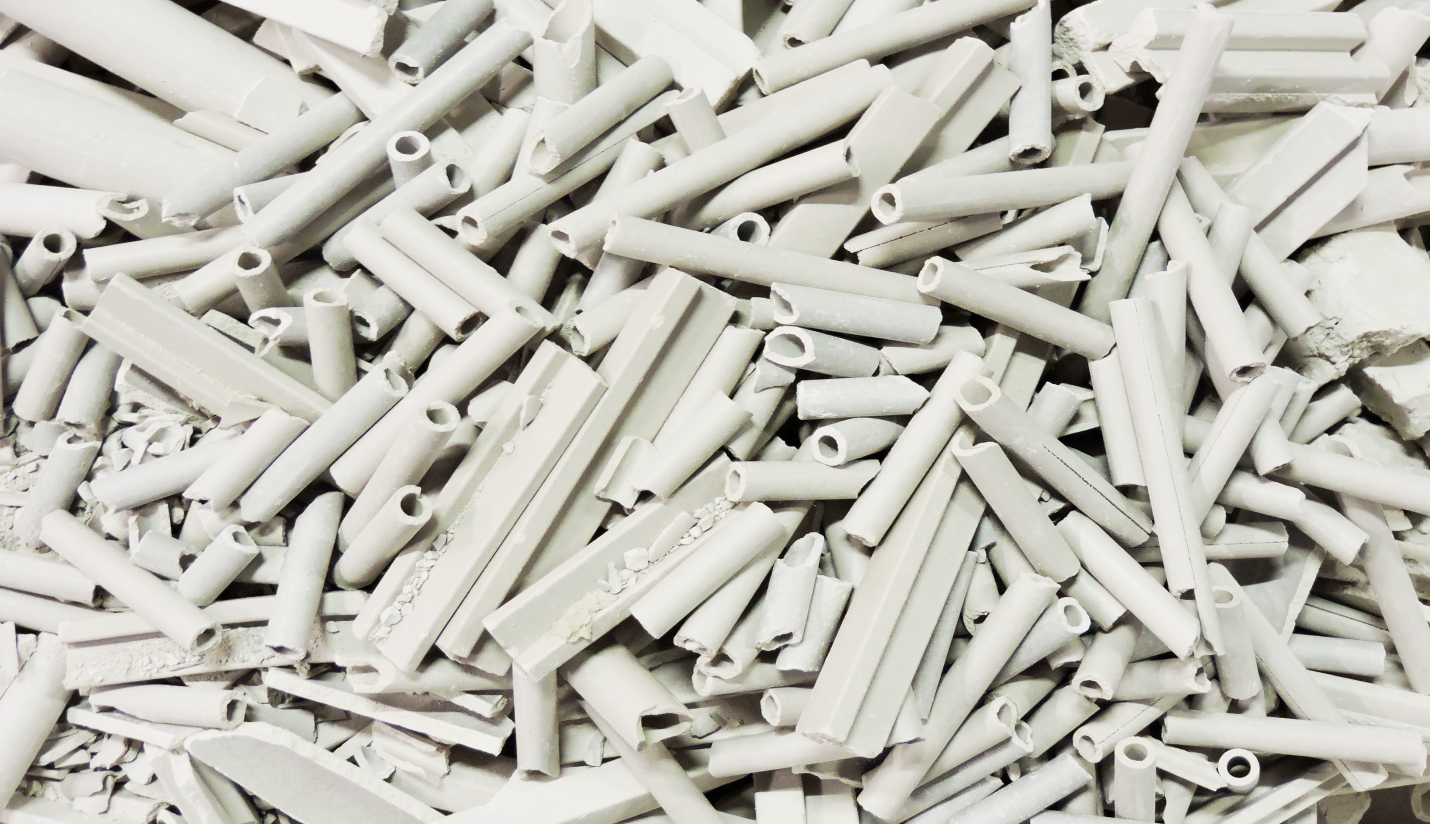
The heat from the furnaces recovered for the comfort of the work environments.
Energy efficiency and the reduction of polluting emissions are two other areas where we have decided to adopt innovative and more sustainable solutions. Between 2020 and 2024, we permanently decommissioned old gas boilers, installed photovoltaic systems, and introduced heat pumps for heating and hydronic systems for cooling. During ceramic firing, a significant amount of heat is generated, which we recover through heat exchangers to warm the factories during the winter.
Regarding polluting emissions, we adopt solutions for smoke recovery and purification. Through post-combustion systems and recuperative burners, the waste gases from high-temperature furnaces are further purified, making them less and less polluting.
An ongoing green evolution, happening step by step.
For us, sustainability is a constant journey, aimed at the continuous improvement of our production processes and the pursuit of maximum efficiency. Replacing outdated machinery, maintaining operational equipment, minimizing urban waste, and reintegrating waste into the production cycle are just a few of the actions we take to move closer to a fully sustainable, low environmental impact circular economy model.